I Am Mother
Film and television • Design • Manufacture • Costumes • Robots and automatons • Robotics and animatronics
I Am Mother
Film and television • Design • Manufacture
• Costumes • Robots and automatons • Robotics and animatronics
She’ll keep you safe. Or will she? Directed by Grant Sputore, with screenplay by Michael Lloyd Green, the sci-fi thriller I Am Mother tells the story of a robot (“Mother”) designed to repopulate the earth after the extinction of humankind. Mother is performed by an actor wearing a complex specialty suit, designed and built by Wētā Workshop.
The project represented an incredible opportunity for the workshop crew. Rather than a static prop, dummy or computer-generated imagery (CGI) creation, Grant’s robot was to function as a fully articulating and emotive character. With the actor driving, Grant’s robot needed to perform.
Senior concept artist Christian Pearce was tasked with imagining what such a robot might look like. The designer experimented with Mother’s form through 2D design, playing with the extremes of proportion and silhouette. As Christian’s design neared its final form, project supervisor Luke Hawker and production manager Kathryn Jackson joined the project to prepare the robot for manufacture.
The challenge lay in hiding a human of flesh and blood inside a rigid robotic structure. From the length of limbs to the choice of materials, every decision would depend on the person inside the suit. Encouraged by the production and casting agent to audition, Luke — a Wētā Workshop crew member of 18 years who is also an experienced actor — landed the role. This, says Kathryn, was “a luxury”. Not only was the performer present for every step; he was leading the project, too.
With Luke cast, the design was modified to match his proportions and the manufacture of Mother began in earnest. Costume technician Bryce Curtis developed a physical prototype from black foam. Sculpted around the performer, this fully articulating prototype was a crucial step towards helping the team marry form, fit and function. The physical prototype was 3D-scanned and modelled by the workshop’s 3D team, led by 3D technicians Joel Savage and Ryan Serrano, and the elements sent to the workshop floor to be fabricated.
The crew approached the build by combining traditional craftsmanship techniques with innovative 3D-printing technology. Components were molded and cast, model-made or 3D printed. From semi-flexible urethane and sintered nylon to cold cast resins and laser-cut plastics, each material was chosen for its balance between durability, comfort, movement and aesthetic.
She’ll keep you safe. Or will she? Directed by Grant Sputore, with screenplay by Michael Lloyd Green, the sci-fi thriller I Am Mother tells the story of a robot (“Mother”) designed to repopulate the earth after the extinction of humankind. Mother is performed by an actor wearing a complex specialty suit, designed and built by Wētā Workshop.
The project represented an incredible opportunity for the workshop crew. Rather than a static prop, dummy or computer-generated imagery (CGI) creation, Grant’s robot was to function as a fully articulating and emotive character. With the actor driving, Grant’s robot needed to perform.
Senior concept artist Christian Pearce was tasked with imagining what such a robot might look like. The designer experimented with Mother’s form through 2D design, playing with the extremes of proportion and silhouette. As Christian’s design neared its final form, project supervisor Luke Hawker and production manager Kathryn Jackson joined the project to prepare the robot for manufacture.
The challenge lay in hiding a human of flesh and blood inside a rigid robotic structure. From the length of limbs to the choice of materials, every decision would depend on the person inside the suit. Encouraged by the production and casting agent to audition, Luke — a Wētā Workshop crew member of 18 years who is also an experienced actor — landed the role. This, says Kathryn, was “a luxury”. Not only was the performer present for every step; he was leading the project, too.
With Luke cast, the design was modified to match his proportions and the manufacture of Mother began in earnest. Costume technician Bryce Curtis developed a physical prototype from black foam. Sculpted around the performer, this fully articulating prototype was a crucial step towards helping the team marry form, fit and function. The physical prototype was 3D-scanned and modelled by the workshop’s 3D team, led by 3D technicians Joel Savage and Ryan Serrano, and the elements sent to the workshop floor to be fabricated.
The crew approached the build by combining traditional craftsmanship techniques with innovative 3D-printing technology. Components were molded and cast, model-made or 3D printed. From semi-flexible urethane and sintered nylon to cold cast resins and laser-cut plastics, each material was chosen for its balance between durability, comfort, movement and aesthetic. Elements such as the robot’s aluminium frame were laser-cut and shaped around the body like a roll cage; others were 3D-printed and built directly into the suit. Worn like gloves but designed like exoskeletons, Mother’s hands were 3D-printed in sintered titanium, complete with sliding elements and grooves to allow movement.
As the build progressed, animatronics supervisor Zoilo Abad worked with technician Rod Sheehy to install more than 700 LED lights and animatronics into the suit. Technician Tim Domett operated the componentry during the shoot, stepping into the role of on-set specialty costume supervisor so that Luke could perform.
While Luke was in front of the camera, Tim was behind it, puppeteering Mother’s facial expressions; a complex choreography designed in collaboration with the director. With Luke and Tim working together, and Zoilo on hand for his technical expertise, the robot’s features came alive. “You could see there was a character in there,” says Luke.
With nearly 300 components designed to Luke’s precise measurements, fabricating Mother was like crafting, constructing, and assembling an elaborate puzzle. Says Christian: “Mother is a pretty technologically dense character — there’s a lot happening in her, lots of new techniques that we hadn’t done before.”
The result was a unique specialty costume that was unlike anything the Wētā Workshop crew had made before. Based under one roof on Wellington’s Miramar Peninsula, design and manufacture combined their creative thinking to realise the filmmakers’ vision.
Elements such as the robot’s aluminium frame were laser-cut and shaped around the body like a roll cage; others were 3D-printed and built directly into the suit. Worn like gloves but designed like exoskeletons, Mother’s hands were 3D-printed in sintered titanium, complete with sliding elements and grooves to allow movement.
As the build progressed, animatronics supervisor Zoilo Abad worked with technician Rod Sheehy to install more than 700 LED lights and animatronics into the suit. Technician Tim Domett operated the componentry during the shoot, stepping into the role of on-set specialty costume supervisor so that Luke could perform.
While Luke was in front of the camera, Tim was behind it, puppeteering Mother’s facial expressions; a complex choreography designed in collaboration with the director. With Luke and Tim working together, and Zoilo on hand for his technical expertise, the robot’s features came alive. “You could see there was a character in there,” says Luke.
The result was a unique specialty costume that was unlike anything the Wētā Workshop crew had made before. Based under one roof on Wellington’s Miramar Peninsula, design and manufacture combined their creative thinking to realise the filmmakers’ vision.
Related projects
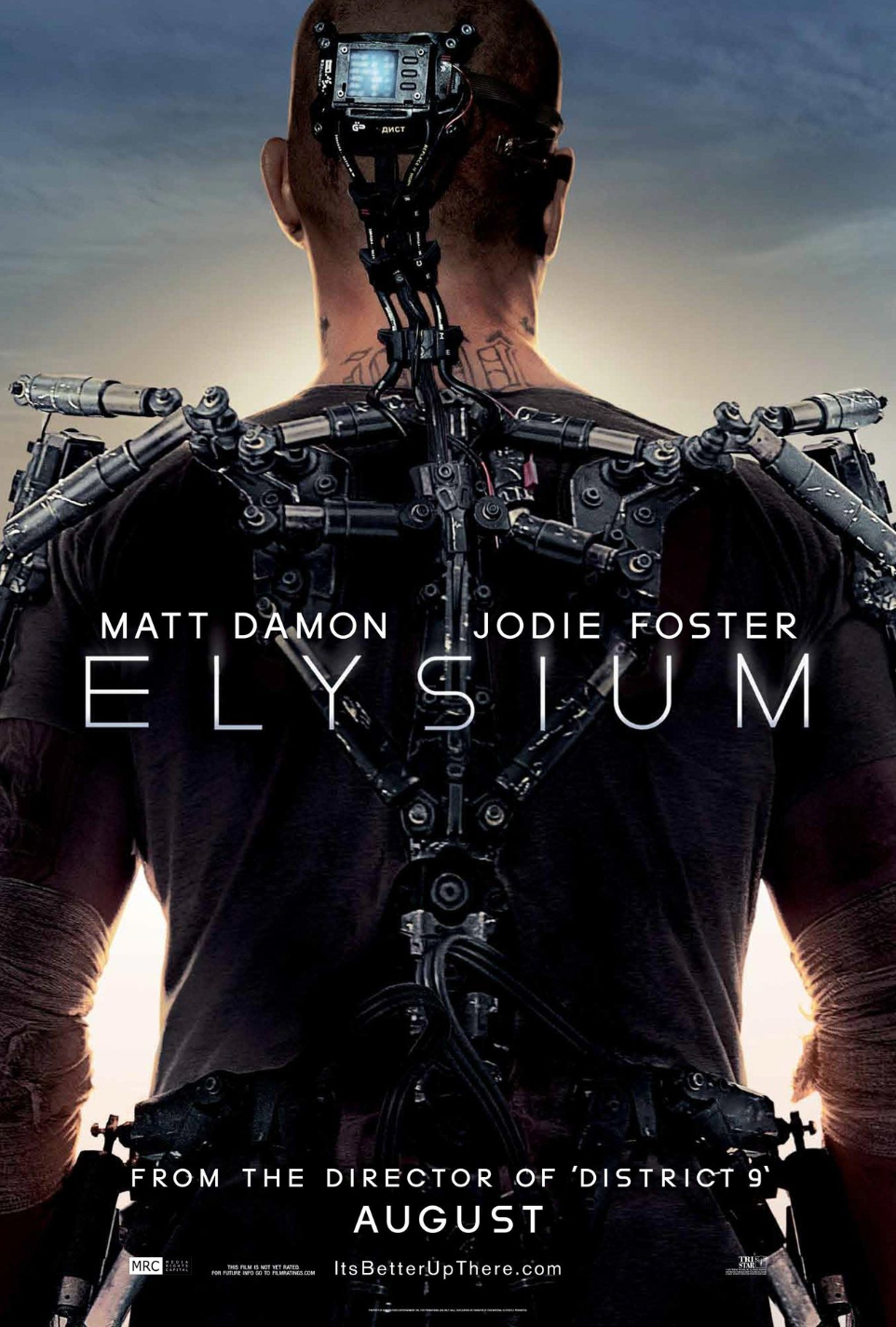
Elysium
Film and television • Design • Manufacture • Costumes • Armour • Props • Weapons • Robotics and animatronics • Life replicas and dummies • World-building
Related projects
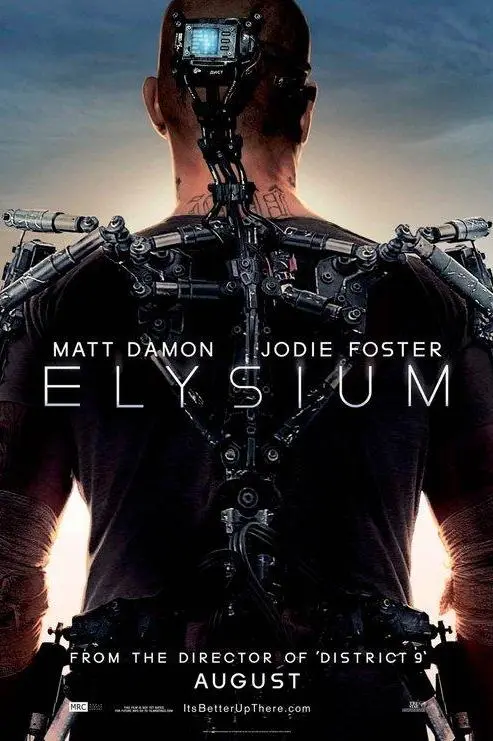
Elysium
Film and television • Design • Manufacture • Costumes • Armour • Props • Weapons • Robotics and animatronics • Life replicas and dummies • World-building